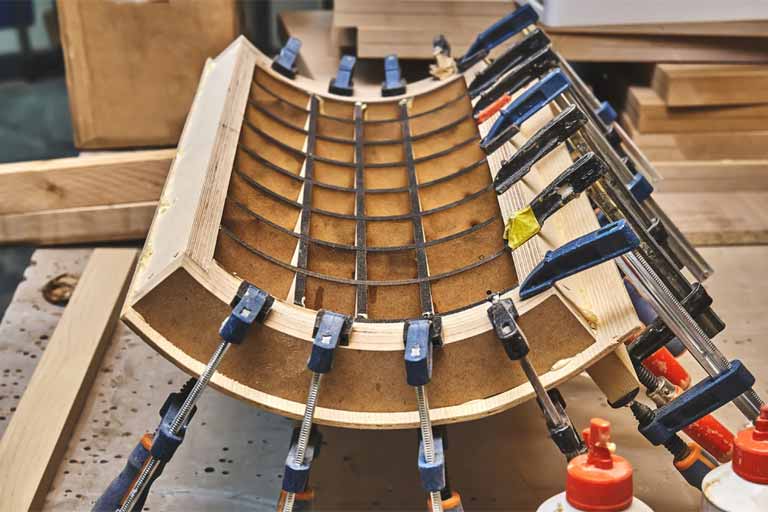
Understanding the Art of Plywood Bending: Unleashing Creative Possibilities
Understanding the Art of Plywood Bending: Unleashing Creative Possibilities
Plywood, a versatile and widely used material, offers a plethora of design opportunities in various industries. Its inherent strength, flexibility, and ability to be shaped have made it a favorite among architects, furniture designers, and artists alike. In this article, we delve into the world of plywood bending, exploring the methods, applications, and benefits of incorporating curved plywood into your projects. By understanding the intricacies of plywood bending, you can unlock a realm of creativity and design innovation.
I. Understanding Plywood and its Properties
To truly comprehend plywood bending, it is essential to grasp the composition and structure of this remarkable material. Plywood consists of multiple thin layers of wood veneers, known as plies, bonded together with adhesives. Each ply is arranged with its grain direction perpendicular to the adjacent plies, resulting in a cross-grain construction. This cross-grain arrangement imparts exceptional strength, stability, and resistance to warping or splitting. Moreover, the alternating grain direction contributes to plywood’s remarkable flexibility, making it ideal for bending applications.
II. Benefits of Bending Plywood
The utilization of bent plywood in design and construction projects offers a myriad of advantages. One of the key benefits is the enhanced aesthetics it brings to the table. The ability to create smooth, flowing curves and organic shapes with plywood adds a touch of elegance and uniqueness to any project. Whether it’s furniture, architecture, or art installations, bent plywood imparts a visually striking and captivating element.
Furthermore, bent plywood expands the realm of design possibilities. Its flexibility allows for the creation of intricate and complex shapes that would be challenging to achieve with other materials. From graceful arches and curved walls to sculptural furniture pieces, plywood bending empowers designers to push the boundaries of their imagination and deliver truly exceptional results.
III. Types of Plywood Suitable for Bending
Not all plywood is created equal when it comes to bending. Certain types and grades of plywood are better suited for curved applications than others. Film-faced birch plywood, for example, with its smooth and durable surface, is a popular choice for creating elegant curves in furniture design. Hexa plywood, renowned for its hexagonal pattern and flexibility, offers a unique aesthetic appeal, making it suitable for both decorative and structural applications.
It is also essential to consider the grades of plywood that exhibit enhanced flexibility. While exterior plywood grades are commonly used for outdoor projects, they can also be employed for bending purposes due to their durability and resistance to moisture. Additionally, laminated birch plywood, with its superior strength and stability, is an excellent choice for more demanding bending applications.
IV. Tools and Equipment for Plywood Bending
Achieving successful plywood bending requires the right tools and equipment. While the specific requirements may vary depending on the chosen bending method, there are some essential tools that every plywood bending enthusiast should have. These include clamps, forms, and steam boxes.
Clamps are crucial for holding the plywood in the desired shape during the bending process. They come in various sizes and styles, such as bar clamps, spring clamps, or C-clamps, providing flexibility and adaptability to different projects.
Forms, whether custom-made or pre-designed templates, serve as guides during the bending process. Custom-made forms offer precise control over the desired shape, while pre-designed forms provide convenience and ease of use, particularly for standard curves or repetitive designs.
For steam bending, a steam box is indispensable. This box creates a controlled environment where the plywood is exposed to steam, softening the wood fibers and making it pliable for bending. Steam boxes can be constructed from various materials, such as PVC pipes or wooden frames, and are equipped with steam generators or steamers to produce the necessary steam.
V. Steam Bending Plywood
One of the most common and traditional methods of plywood bending is steam bending. This technique involves exposing the plywood to steam to make it flexible and pliable for shaping. The steam box is used to enclose the plywood and introduce steam, which penetrates the wood fibers, rendering them soft and easily bendable.
To steam bend plywood, begin by selecting the appropriate plywood and determining the desired shape. Then, prepare the steam box, ensuring it is airtight to retain the steam. Next, heat water in a steam generator or steamer to produce steam. Place the plywood inside the steam box and expose it to the steam for a specific duration, depending on the thickness and type of plywood. Once the plywood has absorbed enough moisture, it becomes malleable and can be carefully bent into the desired shape. Clamps and forms are employed to hold the plywood in place until it dries and retains its new shape.
VI. Kerf Bending Plywood
For those seeking a simpler and less labor-intensive method of bending plywood, kerf bending offers an attractive alternative. This technique involves creating kerf cuts on one side of the plywood, which allows it to bend smoothly along the cuts without the need for steam or excessive heat.
To kerf bend plywood, begin by determining the location and spacing of the kerf cuts, considering the desired bend radius and the thickness of the plywood. Use a saw or a specialized kerf-cutting tool to create evenly spaced, shallow cuts along one side of the plywood. The depth and width of the cuts depend on the plywood’s thickness and flexibility.
Once the kerf cuts are made, carefully bend the plywood along the cuts, applying gentle pressure to prevent breakage. As the plywood bends, the kerf cuts open slightly on the outer side, accommodating the bend while maintaining the integrity of the inner side. Clamps and forms are utilized to hold the plywood in place until it dries and retains its new shape.
VII. Laminating Plywood for Bending
Laminating plywood is a technique commonly employed to achieve more pronounced and complex bends. This method involves layering and gluing multiple thin plywood sheets together, creating a composite material that exhibits enhanced flexibility and strength.
To laminate plywood for bending, begin by selecting thin plywood sheets that are well-suited for bending applications. Apply an appropriate adhesive, such as epoxy or polyurethane glue, evenly on each sheet, ensuring full coverage. Then, stack the plywood sheets together, aligning the grains perpendicular to one another. Apply pressure to the stack, compressing the layers and allowing the adhesive to bond them tightly.
Clamps or a hydraulic press are employed to maintain pressure on the laminated plywood stack until the adhesive cures. The laminated plywood can then be shaped and bent into the desired form using clamps, forms, or other bending techniques. The bonding of multiple thin plywood sheets increases the overall flexibility and durability, enabling the creation of more complex curves and shapes.
VIII. Cold Press Bending Plywood
For those who prefer to avoid heat or steam, cold press bending offers an alternative approach. This technique utilizes hydraulic or mechanical pressure to bend the plywood without the need for moisture or heat.
To cold press bend plywood, begin by selecting the appropriate plywood and determining the desired shape. Construct or acquire a cold press bending machine that can apply even pressure to the plywood. Place the plywood between the forms or molds that represent the desired shape, ensuring that the plywood is adequately clamped and secured.
Activate the hydraulic or mechanical system of the cold press bending machine, gradually applying pressure to the plywood. The pressure will cause the plywood to conform to the shape of the forms or molds, resulting in the desired bend. Leave the plywood clamped in the machine until it dries and retains its new shape. Once the plywood is released from the machine, it will maintain the bent form without the need for additional supports.
IX. Using Forms for Plywood Bending
Forms play a crucial role in plywood bending, as they provide the necessary structure and guidance for achieving specific shapes and curves. Custom-made forms are particularly valuable when aiming for unique or intricate designs.
Custom-made forms are created by shaping or carving a material such as wood, foam, or plastic to match the desired curve or shape. The form should be designed to accommodate the dimensions and curvature of the plywood. It should also allow for clamping or fastening of the plywood to hold it in place during the bending process.
Pre-designed forms, on the other hand, offer convenience and ease of use, especially for standard or commonly used curves. These forms are commercially available and come in various shapes and sizes, catering to different bending requirements. They can be made from durable materials such as metal or plastic, ensuring longevity and repeatable results.
X. Applying Heat for Plywood Bending
Heat can be employed as a supplementary method to enhance the pliability of plywood during bending. By applying localized heat to specific areas, the plywood fibers can soften and become more flexible, facilitating the bending process.
One common technique is the use of a heat gun. A heat gun emits hot air that can be directed towards the plywood to soften the wood fibers. By carefully applying heat to the targeted area, the plywood can be bent more easily without compromising its structural integrity. It is crucial to maintain a safe distance and regulate the temperature of the heat gun to avoid scorching or damaging the plywood.
Alternatively, a torch can be used to apply localized heat. This method requires caution and precision, as the intense heat from the torch can quickly damage the plywood if not handled properly. It is essential to keep the torch moving to distribute the heat evenly and prevent overheating or scorching.
Both heat gun and torch applications should be carried out in a well-ventilated area and with appropriate safety measures, such as protective gloves and eyewear, to avoid potential hazards.
XI. Design Considerations for Bent Plywood
When incorporating bent plywood into design concepts, certain considerations should be taken into account to ensure successful and harmonious outcomes. Integrating the bending capabilities of plywood from the early stages of the design process allows for more cohesive and seamless integration.
Designers should consider the structural implications of bent plywood and ensure that the overall design remains stable and functional. It is vital to strike a balance between aesthetics and structural integrity, as overly complex or ambitious designs may compromise the strength of the plywood.
Furthermore, understanding the limitations and possibilities of plywood bending enables designers to explore innovative applications. Curved plywood can be used to create dynamic furniture pieces, such as chairs with organic shapes or tables with flowing contours. It can also be utilized in architectural structures, such as curved walls or ceiling panels, adding a sense of fluidity and visual interest to the space.
By embracing the bending capabilities of plywood, designers can create truly unique and captivating pieces that stand out in their field.
XII. Common Mistakes and Challenges in Plywood Bending
While plywood bending offers exciting possibilities, it is not without its challenges. Understanding common mistakes and knowing how to overcome them is crucial for achieving successful results.
One common mistake is applying excessive force during bending, which can lead to the plywood breaking or cracking. It is important to bend the plywood gradually and apply pressure evenly to avoid putting undue stress on the wood fibers.
Another challenge is achieving consistent and uniform curves. This requires careful clamping, precise alignment, and attention to detail. Inadequate clamping or misalignment can result in uneven bends or warped shapes.
Overcoming these challenges requires patience, practice, and attention to detail. Taking the time to experiment with different bending techniques, understanding the characteristics of the chosen plywood, and refining the process through trial and error will lead to improved outcomes.
Plywood bending is an art form that unlocks a realm of creativity and design possibilities. Understanding the properties of plywood, the various bending techniques, and the tools involved empowers designers and craftsmen to create remarkable curved structures and furniture pieces. Whether through steam bending, kerf bending, laminating, or cold press bending, plywood can be shaped into graceful curves and intricate forms that captivate the eye. By embracing the art of plywood bending, designers can push the boundaries of their imagination and create truly exceptional works that inspire and delight.