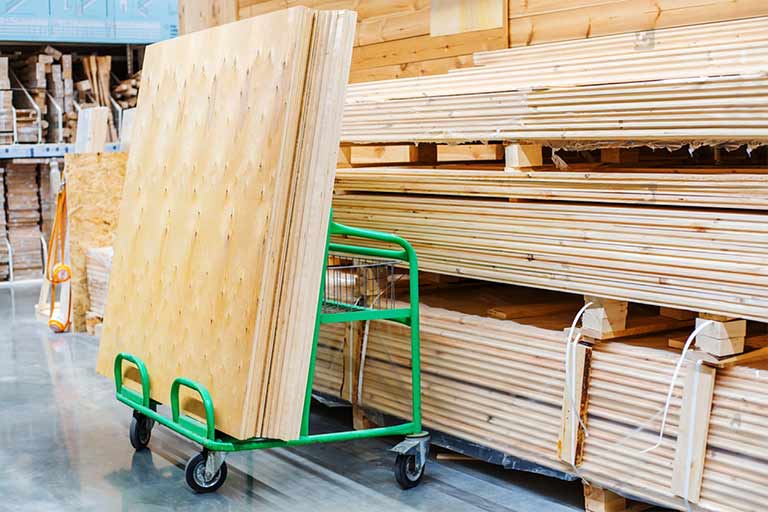
How Plywood is Made: A Step-by-Step Guide
How Plywood is Made: A Step-by-Step Guide
Plywood is a versatile and widely used material in construction and furniture making. It is made by gluing together thin layers of wood veneer, creating a strong and durable sheet material. In this blog post, we will guide you through the step-by-step process of how plywood is made.
Plywood Grades and Uses
Before we dive into the manufacturing process, it’s important to understand the different grades of plywood and their uses. Plywood is graded based on its appearance, strength, and intended use. Exterior plywood, for example, is designed to withstand exposure to the elements, while interior plywood is not. Film faced plywood, also known as hexa plywood, is coated with a layer of film to make it waterproof and ideal for concrete formwork. Hexa flooring is used in industrial and commercial settings due to its durability. UV prefinished plywood is used in high-end furniture and cabinetry due to its smooth surface and resistance to fading.
In addition to these widely known types, there are a variety of other types of plywood with specific uses. For example, plywood for decks is specifically designed for outdoor use and is made with weather-resistant glue. Film faced birch plywood is used in the construction of concrete formwork, offering a smooth and consistent finish. Birch faced plywood is a high-quality option for furniture making due to its strength and durability. Plywood slats are used in bed frames, while thin flexible plywood can be used to create curved surfaces. Patterned plywood can be used to create decorative accents in furniture. Laminated birch plywood is used in boat building due to its strength and resistance to water. Smooth exterior plywood is used in siding, while UV coated plywood is used in cabinetry and high-end furniture.
Manufacturing Process
Plywood is made by peeling thin sheets of wood from a log, then gluing them together in layers with their grains perpendicular to one another. This cross-grain construction gives plywood its strength and durability. After the veneers have been peeled, they are sorted by size and quality. The veneers are then clipped into uniform widths and laid out in a sequence to form a panel.
The next step is to glue the veneers together using a hot press. The glue used can vary depending on the intended use of the plywood. For example, exterior plywood requires a waterproof glue, while interior plywood can use a cheaper, non-waterproof glue. The hot press applies heat and pressure to the veneers, bonding them together into a solid panel.
Once the plywood is bonded, it is trimmed to its final size and sanded to remove any rough spots. The final step is to grade the plywood based on its appearance and quality. The grading system varies depending on the location, but generally, it ranges from A to D, with A being the highest quality and D being the lowest.
Uses of Plywood
Plywood has a wide range of uses in construction, furniture making, and other industries. It is commonly used as a subfloor or underlayment for hardwood flooring, but can also be used as the finished floor itself. Plywood slats are used in bed frames, while thin flexible plywood can be used to create curved surfaces. Film face ply and patterned plywood can be used to create decorative accents in furniture. Laminated birch plywood is used in boat building due to its strength and resistance to water. Smooth exterior plywood is used in siding, while UV coated plywood is used in cabinetry and high-end furniture.
At SFK Plywood, we offer a wide range of plywood grades and products, including birch faced plywood and exterior plywood grades. Birch faced plywood is a high-quality option for furniture making due to its strength and durability. Exterior plywood is made with weather-resistant glue and is ideal for outdoor use, such as decks and siding. Our film faced birch plywood offers a smooth and consistent finish, making it ideal for concrete formwork. Our hexa flooring is perfect for industrial and commercial settings due to its durability. We also offer UV-coated plywood for high-end furniture and cabinetry, as well as laminated birch plywood for boat building.
Plywood is a versatile and widely used material that is essential in construction and furniture making. Understanding the manufacturing process and the different grades and uses of plywood can help you choose the right material for your project. At SFK Plywood, we are committed to providing high-quality plywood products to meet your specific needs. Contact us today to learn more about our products and how we can help you with your next project.
If you have any questions or want to know more about plywood wholesale, do not hesitate to call us or fill up the form on our website. As a leading plywood wholesale supplier, we are always happy to assist you.
Frequently Asked Questions
Can you glue down hardwood flooring to plywood?
Yes, you can glue down hardwood flooring to plywood. Plywood is a common subflooring material for hardwood flooring.
What is plywood used for?
Plywood is used for a wide range of applications, including subflooring, underlayment, furniture making, and decorative accents.
How is plywood converted?
Plywood is made by gluing together thin layers of wood veneer, creating a strong and durable sheet material.
How are plywood boards manufactured?
Plywood boards are manufactured by peeling thin sheets of wood from a log, then gluing them together in layers with their grains perpendicular to one another.
What machines are used to make plywood?
The machines used to make plywood include veneer peeling machines, hot presses, and sanders.
What method of construction is plywood?
Plywood is made using cross-grain construction, in which the grain of each layer of veneer is perpendicular to the layer above and below it.
How is plywood engineered?
Plywood is engineered by bonding together thin layers of wood veneer to create a strong and durable sheet material.